Meta Description
Explore the scientific and practical reasons behind the industry’s preference for opaque photocell housings, including UV resistance, sensor accuracy, and long-term durability. Learn why transparent designs, though visually appealing, compromise performance.
Introduction
At first glance, transparent photocell housings may appear modern and visually appealing. However, professional manufacturers consistently prefer opaque or semi-transparent designs in high-quality applications. This preference stems from crucial engineering considerations, material science principles, and decades of field experience. Below, we will analyze the technical rationale behind this industry standard, supported by optical, material degradation mechanisms, and sensor performance requirements.
Functional Requirements of Photocell Housings
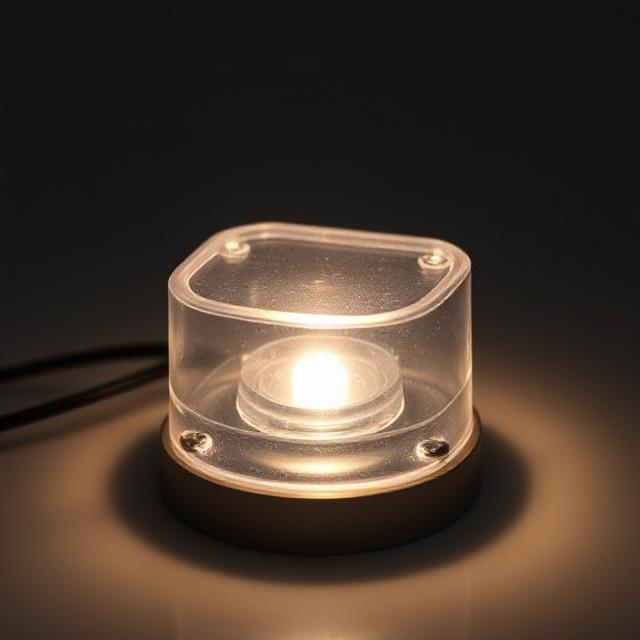
Photocell housings are not just decorative; they are the first line of defense for sensitive light sensing systems. Key functional requirements include:
Environmental Protection
- Must withstand UV radiation, thermal cycles (-40°C to +85°C), and have IP65/67 water resistance.
- Prevent ingress of dust, moisture, and corrosive contaminants such as industrial SO₂ and coastal salt air.
Optical Performance
- Maintain consistent light transmission (±5% error) across the 400-700nm visible spectrum.
- Eliminate stray light paths (e.g., from car headlights, adjacent streetlights’ reflections).
Material Stability
- Prevent yellowing (ΔYI < 2 after 3,000 hours of ASTM G154 QUV test).
- Retain mechanical strength (tensile strength >60 MPa) even after 10 years of outdoor exposure.
Security
- Opaque designs prevent reverse-engineering of circuit layouts and tampering.
Major Drawbacks of Transparent Housings
Light Interference and Sensor Failure
Transparent housings create uncontrolled light paths that severely affect sensor accuracy:
Multiple Path Reflections
Internal surfaces (housing walls, PCB, components) create unintended reflection interfaces. For example, a 2mm thick polycarbonate housing with a refractive index of n=1.58 reflects about 8% of incident light, generating noise signals equivalent to 0.5-2 lux, which could trigger false dawn/dusk detection.
Glare Amplification
Lambertian scattering from surface imperfections disperses ambient light (e.g., headlights with brightness over 1,000 lux) onto the photodiode. Opaque black housings absorb scattered photons, maintaining noise levels below 0.1 lux.
Case Study: In some China municipal lighting trials conducted in 2022-2023, transparent-housing devices experienced 23% false triggers, whereas opaque designs had only 0.2%.
Accelerated Material Degradation
Transparent polymers inherently face UV fragility:
Photochemical Degradation
UV photons (300-400nm) break down polymer chains. Polycarbonate’s carbonate groups absorb strongly between 290-330nm, leading to chain cleavage. Untreated transparent polycarbonate loses 50% of its tensile strength within 2 years, while UV-stabilized black polycarbonate can last over 8 years.
Surface Erosion
Due to thermal expansion (ΔT = 60°C daily fluctuation) and UV-induced embrittlement, transparent materials develop micro-cracks, through which moisture enters, accelerating hydrolysis.
Accelerated Testing Data:
- Material | Time to Reach 50% Cloudiness (QUV-B) | Yellowing Index (ΔYI) @1,000 hours
- Transparent PC | 700 hours | 15.2
- Black UV-PC | 3,500 hours | 1.8
Maintenance and Aesthetic Failures
Visibility of Contaminants
Airborne particles (PM2.5/PM10) electrostatically adhere to transparent surfaces. A 1μm dust layer can reduce light transmission by 12-18%, requiring frequent cleaning. Other housings do not face this issue.
Engineering Advantages of Opaque/Semi-transparent Designs
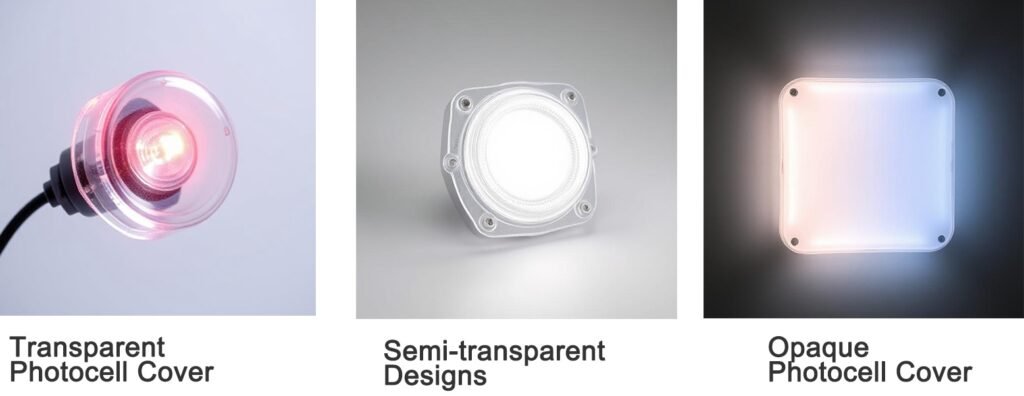
Precise Light Management
Wavelength Filtering
Black polycarbonate acts as a long-pass filter, blocking UV and infrared rays while transmitting 500-650nm wavelengths, which match the sensitivity of CdS/LDR sensors.
Directional Light Paths
Opaque baffles limit the incident angle to ±30°, aligning with the cosine correction requirement for photodiodes.
Enhanced Durability
UV Absorption
Carbon black additives absorb 99.9% of UV light (wavelengths under 400nm), making its lifespan 4-5 times longer than transparent materials.
Thermal Management
Black surfaces emit infrared radiation at 94% emissivity (ε=0.94), reducing internal temperatures by 8-12°C compared to reflective transparent materials.
Tamper Resistance
Opaque housings prevent direct inspection of:
Potentiometer settings (prevent unauthorized adjustments)
Circuit board layouts (IP protection)
Conclusion and Recommendations
Transparent photocell housings compromise performance through optical interference, accelerated material degradation, and security risks. For critical applications, opaque or black-translucent housings are recommended, particularly in harsh environments.
Zhejiang Leadtop Electrical Co., Ltd. primarily uses opaque or black-translucent materials, such as blue, green, yellow, black, and orange, offering excellent UV resistance and durability. If you would like to learn more about photocell technology or have any questions, feel free to contact us at leaditop.com or email us at info@leaditop.com.